In the world of engineering and material science, mechanical testing plays a crucial role in evaluating the mechanical properties of materials. Mechanical testing is like giving materials a check-up to determine the strength of materials to evaluate their durability, mechanical testing serves as a fundamental tool for engineers. It helps engineers understand how materials will behave in different situations, so they can make sure everything from buildings to cars to everyday objects is safe and reliable. In this guide, we’ll explore the What is mechanical testing, its importance, and the different types of mechanical testing used to measure different properties of materials.
What is Mechanical Testing?
Mechanical testing is a process used to evaluate the mechanical properties of materials, providing valuable insights into how they will perform under various conditions. These properties include strength, hardness, elasticity, toughness, and more. By subjecting materials to controlled tests, engineers can understand their behaviour and make informed decisions in material selection, design, and manufacturing processes.
Types of Mechanical Testing
Tensile Testing:
Tensile testing is a type of mechanical testing used to understand how strong and stretchy material is. Imagine you have a rubber band, and you want to know how much you can stretch it before it breaks. That’s what tensile testing does but with all sorts of materials like metal, plastic, or fabric.
During the test, a small piece of the material, called a specimen, is pulled apart with a machine. As the machine pulls, it measures how much force is needed to stretch the material and how much the material stretches. This helps engineers figure out important things like how strong the material is (its strength) and how much it can stretch before breaking (its elasticity).
Tensile testing is crucial because it helps engineers choose the right materials for building things like bridges, airplanes, or even everyday items like chairs and tables. It ensures that these materials can handle the stresses they’ll face in real-life situations, keeping us safe and secure.
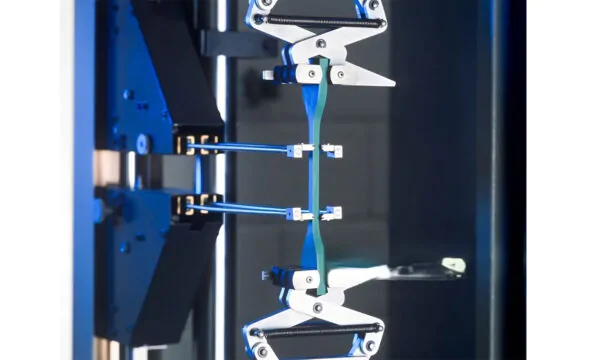
For example,
let’s say you’re designing a bridge. You’d want to know how strong the steel cables are that hold the bridge up. Tensile testing helps engineers figure out if the cables can handle the weight of cars and trucks driving over the bridge without snapping.
Common standards for the tensile test include ASTM E8/E8M (Standard Test Methods for Tension Testing of Metallic Materials), ISO 6892-1 (Metallic Materials), ASTM D638(Standard Test Method for Tensile Properties of Plastics), ASTM D412(Vulcanized Rubber and Thermoplastic Elastomers)
Compression Testing:
Compression testing applies force to compress a material, measuring its ability to withstand crushing forces. It’s commonly used to assess the compressive strength and stiffness of materials.
Here’s how it works: Imagine you have a block of foam. You place the foam block between two plates in a machine. Then, the machine pushes the plates together, applying more and more force until the foam squishes.
As the machine pushes, it measures how much force is needed to crush the foam and how much the foam squishes. This tells us important things about the material, like its compressive strength (how much force it can take before being crushed) and its stiffness (how much it resists being squished).
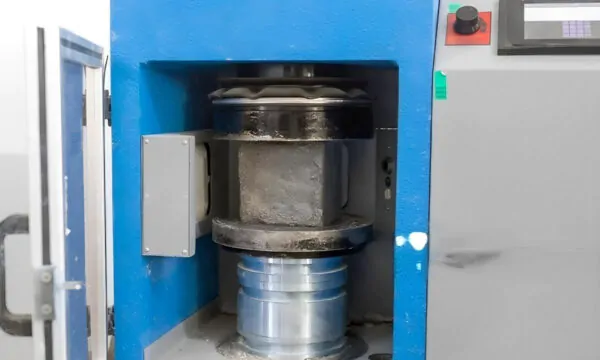
For example,
in construction, engineers might use compression testing to make sure concrete blocks are strong enough to support the weight of a building without crumbling under pressure.
Common standards for the Compression test include ASTM E9(Test Methods of Compression Testing of Metallic Materials at Room Temperature), ASTM D695(Test Method for Compressive Properties of Rigid Plastics), ASTM D1621(Compressive Properties of Rigid Cellular Plastics), BS EN ISO 604(Plastics – Determination of Compressive Properties)
Fracture Mechanics Testing
Fracture mechanics testing is like detective work for materials. It helps engineers understand how materials break and why. Imagine you’re investigating a crime scene where something broke – maybe a bridge, a car part, or even a simple household item. Fracture mechanics testing helps engineers figure out what caused the break and how to prevent it from happening again.
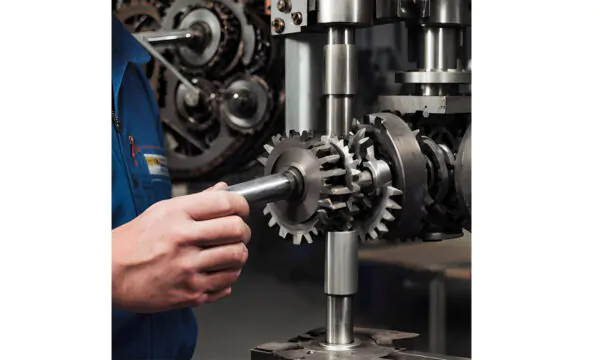
Here’s how it works: Engineers take a broken piece of material and examine it closely, like a detective looking for clues. They might use special tools to measure things like the size and shape of the crack, how fast it grew, and what direction it spread. This information helps them understand the material’s behaviour under stress and identify any weaknesses or flaws that led to the break.
By studying fractures in this way, engineers can improve designs, choose better materials, and make products safer and more reliable. It’s like solving a mystery to protect people and property from future accidents.
Common standard for the Fracture Mechanics Testing includes ASTM E399, ASTM E1820, ASTM E1921, ASTM E1823, ASTM D5045, ISO 12135
Flexural Testing:
Flexural testing, also known as bend testing, is like giving a material a gentle bend to see how flexible and strong it is. It’s a mechanical test used to measure a material’s resistance to bending or flexing.
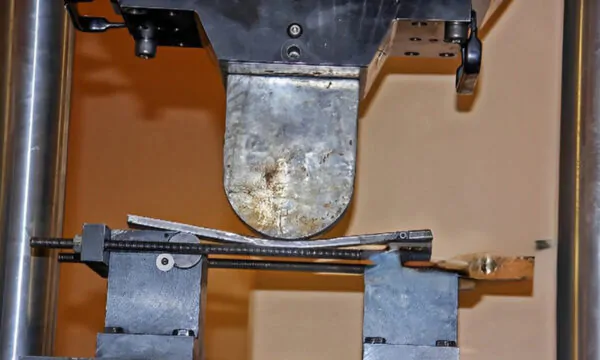
Here’s how it works: Imagine you have a thin piece of wood or a plastic ruler. You place it across two supports, like a mini bridge, and apply a force to the middle of the ruler. As you push down, the ruler bends or flexes and the machine measures how much it bends and how much force it takes to bend it.
Flexural testing helps engineers understand how materials behave when subjected to bending forces, which is important for designing things like beams, bridges, or even everyday items like plastic containers or metal rods. By knowing how much a material can bend before breaking, engineers can design structures and products that are strong and durable enough for their intended use.
Common standard for the Flexural Testing includes ASTM D790, ASTM C1161, ASTM D6272
Impact Testing
Impact testing is like giving a material a sudden hit or shock to see how it reacts. It’s a mechanical test used to measure a material’s ability to absorb energy when subjected to sudden impact or shock loads.
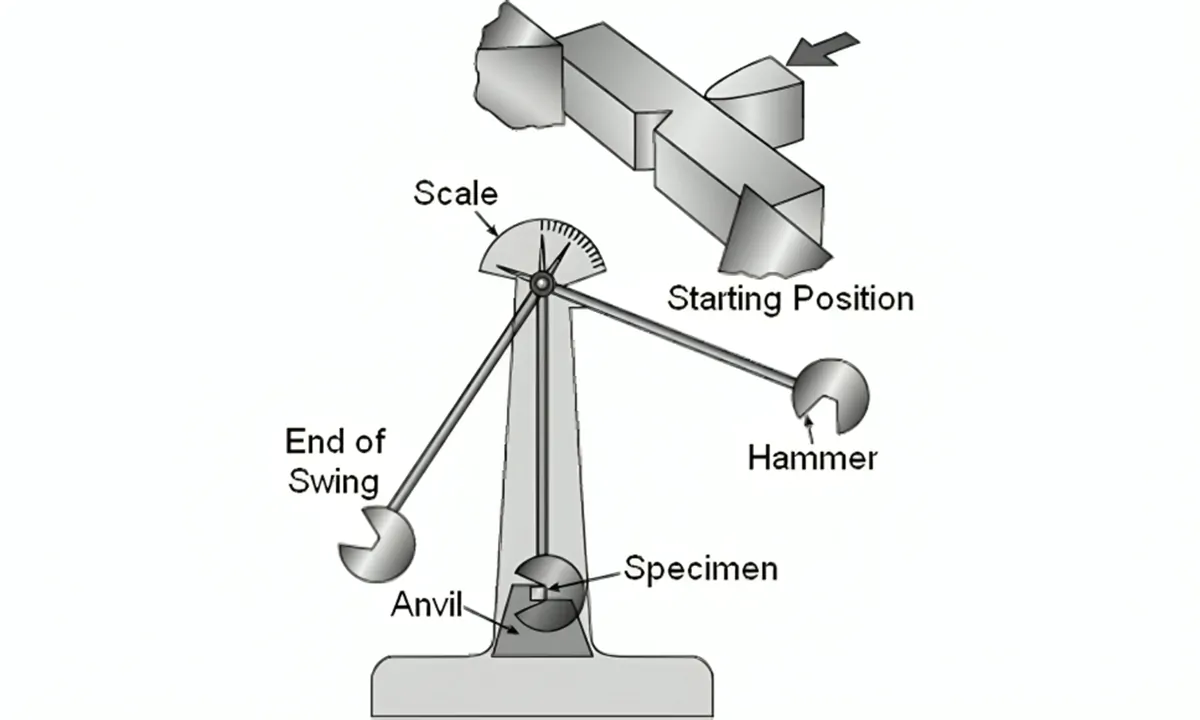
Here’s how it works: You have a material, like a metal or plastic sample, and you give it a quick hit with a swinging hammer or a falling weight. The test measures how much energy the material can absorb before breaking or cracking.
Common types of impact testing include:
- Charpy Impact Test: Imagine swinging a small hammer at a notched piece of metal. The Charpy test measures how much energy the metal can absorb before breaking. It’s like checking how tough the metal is when hit.
- Izod Impact Test: Similar to Charpy, but the metal piece is held vertically. It helps see how much energy the metal can absorb when struck differently.
Impact testing helps engineers understand how materials behave when they’re hit or bumped, which is important for designing things like car bumpers, helmets, or even smartphone cases. By knowing how much energy a material can absorb before breaking, engineers can design products that protect people and objects from impacts and accidents.
Common standard for the Flexural Testing includes ASTM E23, ASTM D256, ISO 179
Hardness Testing
Hardness testing is like giving a material a “toughness check” It helps engineers understand how resistant a material is to being scratched, indented, or deformed. Imagine you’re testing how hard a diamond is compared to a piece of wood – that’s where hardness testing comes in.
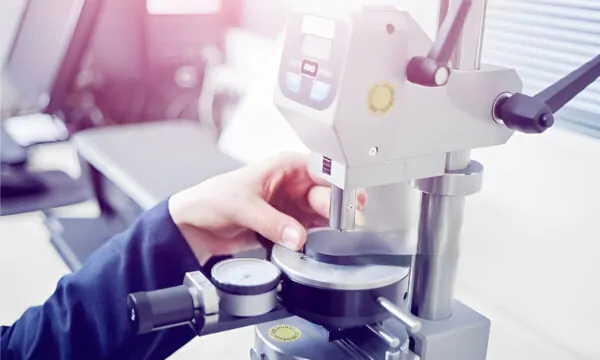
Here’s how it works: You have a small sample of the material, and you apply a known amount of force to it using a special tool, like a pointed tip or a small ball. The test measures how much the material resists being penetrated or deformed under this force.
Types of Hardness Testing, including:
- Rockwell Hardness Test: In this test, a hard indenter is pressed into the material under a specific load, and the depth of indentation is measured. The Rockwell hardness is indicated by a numerical value on a scale.
Rockwell Hardness Test - Brinell Hardness Test: A hardened steel ball is pressed into the material under a specified load, and the diameter of the indentation is measured. Brinell hardness is calculated based on the applied load and the diameter of the indentation.
Brinell Hardness Testing Machine - Vickers Hardness Test: Like the Brinell test, but a square-based pyramid-shaped diamond is used as the indenter. Vickers hardness is determined by measuring the diagonal lengths of the indentation.
- Mohs Hardness Scale: This scale ranks materials from softest to hardest based on their scratch resistance. For example, talc is the softest at 1, whereas diamond is the hardest at 10.
- Knoop Hardness Test: Like the Vickers test, but a diamond indenter with a rhombic-based pyramid shape is used. Knoop hardness is calculated based on the applied load and the length of the indentation.
Each type of hardness test has its advantages and is suitable for different materials and applications. By performing hardness testing, engineers can ensure that materials meet the required specifications and are suitable for their intended use.
A common standard for Hardness Testing includes ASTM E10, ASTM E384, ISO 6508, and ISO 6506.
Fatigue Testing
Fatigue testing is like giving a material a “tiredness check.” It helps engineers understand how a material behaves when it’s repeatedly stressed or loaded repeatedly. Imagine you’re bending a paperclip back and forth until it breaks – that’s a bit like what fatigue testing does but on a larger scale for different materials.
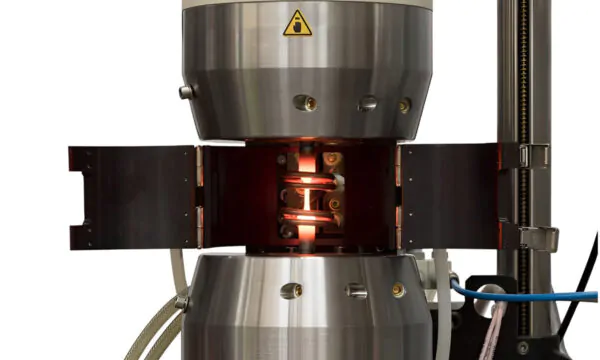
Here’s how it works: You take a sample of the material, like a metal rod or a plastic part, and you apply loads to it in a repetitive way. This could be bending, stretching, or compressing the material repeatedly. The test measures how many cycles the material can endure before it breaks.
Fatigue testing is crucial for things that go through a lot of stress in their lifetime, like aeroplane wings, car parts, or even the springs in your mattress. By understanding how a material holds up under repeated stress, engineers can design products that last longer and are less likely to fail over time.
Common standard for the Fatigue Testing includes ASTM E466, ASTM E606 / E606M, ASTM E647, ISO 1099, ISO 12107
Torsion Testing
Torsion testing is like twisting something to see how it holds up. It helps engineers understand how materials react when they’re twisted or torqued. Imagine you’re twisting a wet towel to wring out the water – that’s like what torsion testing does but on different materials.
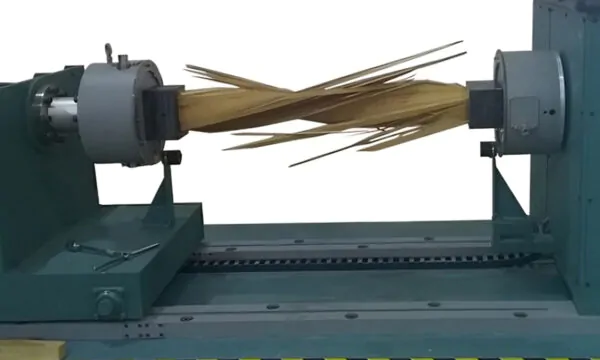
Here’s how it works: You take a sample of the material, like a metal rod or a plastic tube, and you apply a twisting force to it. The test measures how much the material twists and how it responds to the force.
Torsion testing is crucial for things like shafts, screws, and gears that experience twisting forces in real-world applications. By understanding how a material responds to torsion, engineers can design stronger and more durable products that can handle twisting without breaking or deforming.
A common standard for Torsion Testing includes ASTM E1434, ISO 7800, and ISO 16803.
Creep Testing
Creep testing is like checking how a material slowly changes shape over time when it’s under constant stress. It helps engineers understand how materials behave when they’re exposed to prolonged loads or stress. Imagine you’re stretching a rubber band and watching how it gradually gets longer – that’s a bit like what creep testing does but for different materials.
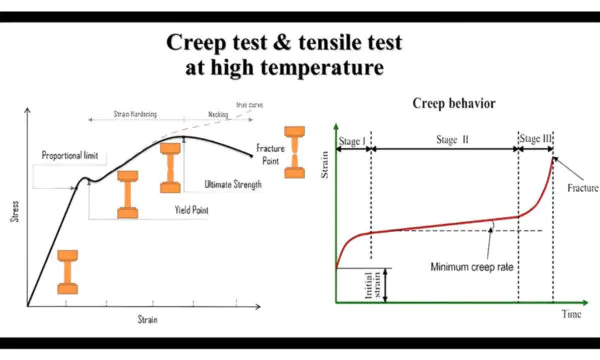
Here’s how it works: You take a sample of the material, like a metal rod or a plastic sheet, and you apply a constant load or stress to it. Then, you observe how the material deforms or stretches over a long period.
Creep testing is important for materials used in situations where they’ll be under constant stress for extended periods, like bridges, pipelines, or turbine blades. By understanding how a material responds to long-term stress, engineers can create structures and products that are safe and reliable over time.
A common standard for Creep Testing includes ASTM E1450, ASTM E292, and ISO 204.
Corrosion Resistance
Corrosion resistance is like giving a material a “rust check.” It measures how well a material can withstand damage caused by chemical reactions to its environment, like rusting or corroding.
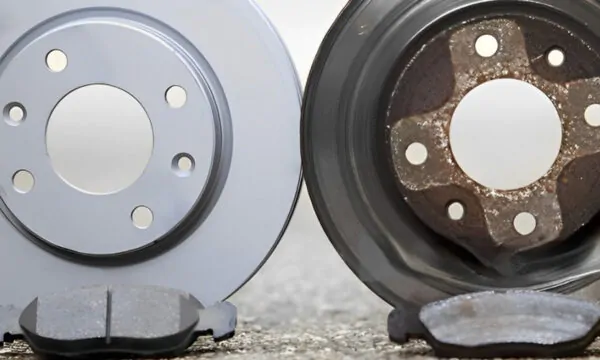
Here’s how it works: When materials are exposed to things like moisture, salt, acids, or other corrosive substances, they can start to break down and deteriorate. Corrosion resistance testing evaluates how resistant a material is to these processes. It might involve exposing a sample of the material to harsh conditions for a set period and then assessing any damage or changes that occur.
Corrosion resistance is critical for materials used in environments where corrosion is likely to occur, like outdoor structures, pipelines, or marine equipment. By selecting materials with good corrosion resistance, engineers can ensure that products last longer and require less maintenance over time.
Common standard for the Corrosion resistance Testing includes ASTM G31, ASTM G71, ASTM B117, ISO 9227, ISO 9223
Non-destructive testing
Non-destructive testing (NDT) is like giving a material a “health check” without harming it. It’s a way to inspect and evaluate materials, components, or structures for defects or irregularities without causing damage.
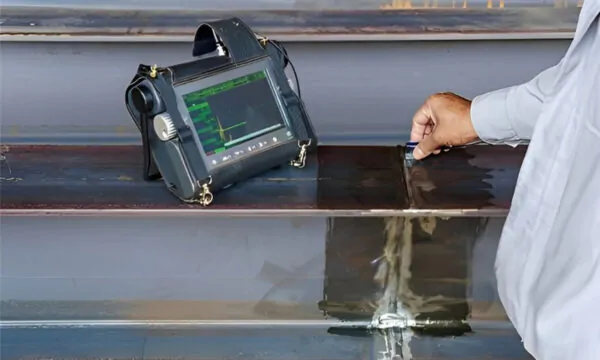
Here’s how it works: Instead of breaking apart or altering the material, NDT methods use various techniques to examine its properties and detect flaws. These techniques can include visual inspection, ultrasonic testing, radiographic testing, magnetic particle testing, and many others.
NDT is crucial for ensuring the safety, reliability, and quality of products and structures in industries like aerospace, automotive, construction, and manufacturing. By identifying defects early without damaging the material, engineers can make informed decisions about repair, maintenance, or replacement, ultimately saving time and costs.
Common standards for Non-destructive testing include Ultrasonic Testing (UT), Radiographic Testing (RT), Magnetic Particle Testing (MT), Liquid Penetrant Testing (PT)
What is the Importance of Mechanical Testing?
Mechanical testing is super important because it helps us understand how different materials will perform in real life.
That’s where mechanical testing comes in. By putting materials through tests like pulling them apart, squishing them, bending them, or hitting them, we can figure out how strong they are, how much they can bend, or how they’ll react to being hit.
Mechanical Testing helps engineers:
- Choosing Materials: Engineers need to pick the right materials for their projects. Mechanical testing tells them how strong, flexible, or tough materials are, so they can choose the best ones.
- Making Designs Better: By testing materials, engineers can figure out how to make designs stronger, safer, and more reliable. For example, they can make sure bridges can hold up heavy trucks or that airplane wings won’t break during flight.
- Checking Quality: Mechanical testing helps engineers make sure that materials and products are made well. They can test samples to make sure they meet quality standards and are safe to use.
- Understanding Failures: If something breaks unexpectedly, engineers can use mechanical testing to figure out why. This helps them fix problems and make things better next time.
- Product Development: When developing new products or prototypes, engineers use mechanical testing to assess the performance and durability of different materials and designs. This ensures that the final product will meet or exceed customer expectations.
- Compliance with Standards: Many industries have specific standards and regulations that materials and products must meet. Mechanical testing helps engineers ensure that their designs and materials comply with these standards, ensuring safety and regulatory compliance.
- Cost Efficiency: By accurately predicting how materials will behave in real-world conditions, engineers can avoid over-engineering (using more material than necessary) or under-engineering (using inadequate materials), leading to cost-effective solutions.
This information is crucial for engineers, it helps them choose the right materials for different jobs, make sure products are safe, and even improve designs to make things better and stronger. So, mechanical testing helps us build safer, more reliable stuff!
In conclusion,
Understanding mechanical testing and its various types is crucial for ensuring the quality and durability of materials we use every day. Whether it’s checking how strong a metal is or making sure a plastic component can handle repeated stress, these tests help create safer and more reliable products.
If you’re looking for the Best mechanical testing services, consider reaching out to Getra Innovation. Their expertise in mechanical testing can provide valuable insights into the performance and reliability of materials, ensuring that your products meet the highest standards. Invest in quality testing to build a stronger and more resilient future!
FAQs
Q: Why is Mechanical Testing important?
A: Mechanical testing is important because it helps ensure the quality, safety, and reliability of materials used in products and structures. It allows engineers to understand how materials will perform in real-world situations.
Q: What are the different types of mechanical testing?
A: The main types of mechanical testing include tensile testing, hardness testing, impact testing, fatigue testing, and corrosion resistance testing.
Q: How is mechanical testing done?
A: Mechanical testing is conducted by applying controlled forces to materials using specialized equipment. The process involves preparing specimens, applying loads, collecting data, analyzing results, and documenting findings.
Q: Where can I find reliable mechanical testing services?
A: Getra Innovation offers comprehensive mechanical testing services to help businesses assess the properties and performance of materials used in their products.